The tool set began to grow for the project in general. I returned the pos $15 weller and picked up a velleman vtss5u at fry's for $20. Not much more cash, but the iron is so much better. I picked up some terminal strips to organize the wires, some bolts that fit the mounting plate well enough and some more 22 awg wire. Still can't find a good crimper that will strip 22 awg - despite them saying 20-22 on them, 22 just slips right through. They sell some decent strippers that you can change the size by nut, it's just not practical if you're working with more than 1 size wire - which isn't the case here so I picked one of those up as well. It'd just be nice to have a crimper/stripper/cutter all in one that actually stripped 22awg.
Here's the crap table
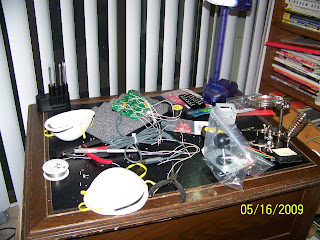
I also picked up a pair of helping hands from radio shack that went a long way. There's a good size magnifying glass on it and alligator clips to hold your work. With a little experience under my belt the solder job was much easier this go around. The 360 retro arcade stick($9@gamestop) was an easier to work with pcb as well with nice holes next to the signals to put the wire through and solder in. It's large enough to not make the work so nerve racking as well. Here's a look at the finished job, which I don't actually mind showing vs the old dc pcb(that was a wreck). The only mistake I made was putting the Y button on the ground vs the signal below it. A quick resolder fixed that problem and I could see in windows the buttons were all functioning well.
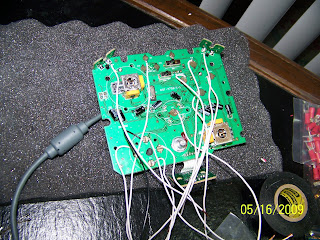
Back to the case problem at this point. We took an afternoon and went to a few craft stores as well as wally world to look for a better solution than another shoe box type. There's a lot of briefcase sticks out there as well as tupperware, that's what we kept our eyes out. Having not much luck I found a plywood box at Michael's for $6. For the record I would not suggest using one as the top and bottom panels aren't even a quarter inch thick. Living in an apartment limits my woodworking tools/options, so I settled on the craftbox despite this problem. I also picked up a 24mm and 30mm drillbit for the button holes versus eyeballing it.
With a few print outs from slagcoin.com I chose the panel layout and went to town on this tiny box.
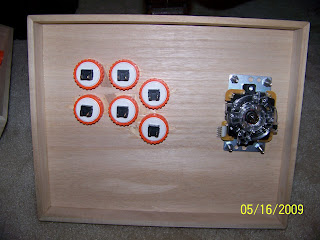
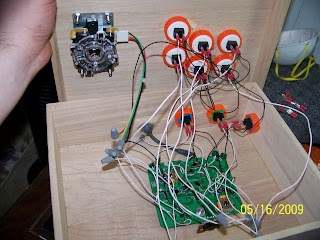
At this point I realized I never came up with a solution for the headset port. I've yet to bother with it, as this case like the previous is a temporary solution until I can make/find another. Here's a few snapshots of the finished product sanded down on the sides and edges but left unstained(which was another mistake).
Top view:
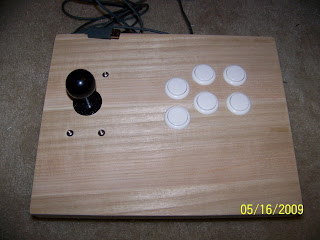
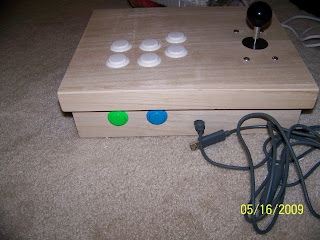
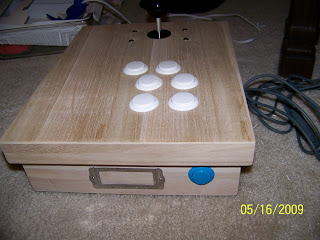
So with the second attempt finished I'm feeling a lot more confident in my pcb work. I have a long way to go as far as cases, as I've yet to actually build one. The craftbox was a decent start for looking at layouts and understanding spacial limitations within. Staining the wood is a must. Within a day the plywood began absorbing the oil from my hands and has left it nice and ugly to look at where they rest next to the stick and buttons. Again a common sense issue I simply didn't care to remedy. Patience will go a long way in crafting a real box, as the entire project would have benefited from such a simple thing. I also would chose a different panel layout the next time around as there isn't much space to rest my left hand with the stick being so far out from the buttons. Again I would stress triple checking your materials prior to starting.
I'm heading out to Texas next week to visit family....and there's a garage! So I'll keep notes and take pics of what we come up with out there. It should be interesting.